联系人鲍先生
润滑油系统中的润滑油通常是强迫循环运行方式,运行中经常进入一些空气,在激烈搅动的情况下会产生泡沫和气泡,较大的空气泡能迅速上升到油的表面,而较小的气泡上升较慢。无论以哪种形式存在于油中都会对设备带来不良影响,可能使油泵油压上不去而影响油的循环、破坏油膜、发生磨损,同时油压不稳,影响调节,严重时泡沫由油箱顶部外溢,威胁机组运行,所以油品具有抗泡沫性能。
为了消除工作介质在设备系统工作时产生的泡沫,经过长期的观察和研究, 找到了多种消泡的方法,如物理消泡法、机械消泡法、化学消泡法等,其中的化学消泡法中的加入抗泡剂效果好,方法简单,因此,被国内外广泛采用。1943年壳牌发展公司和海湾研究发展公司同时发现液态有机聚硅氧烷是非常有效的抗泡剂。现在甲基硅油仍广泛用作润滑油抗泡剂。
甲基硅油作抗泡剂,与它的以下性质有关:
①表面张力比润滑油低,促使发泡剂脱附,但它本身形成的表面膜强度较差;
②它在润滑油中溶解度小,但又有一定的亲油性;
③化学性质不活泼,不易与润滑油发生化学反应;
④用量低,效果好,即使在高温时也能有效地消除润滑油中的泡沫;
⑤甲基硅油具有挥发性低、粘温性好、闪点高、凝固点低、热稳定性好,使用寿命长的优点。在润滑油中起消泡作用的二甲基硅油常用粘度是(25℃运动粘度)100-100000cs,使用量为5-50mg/kg。
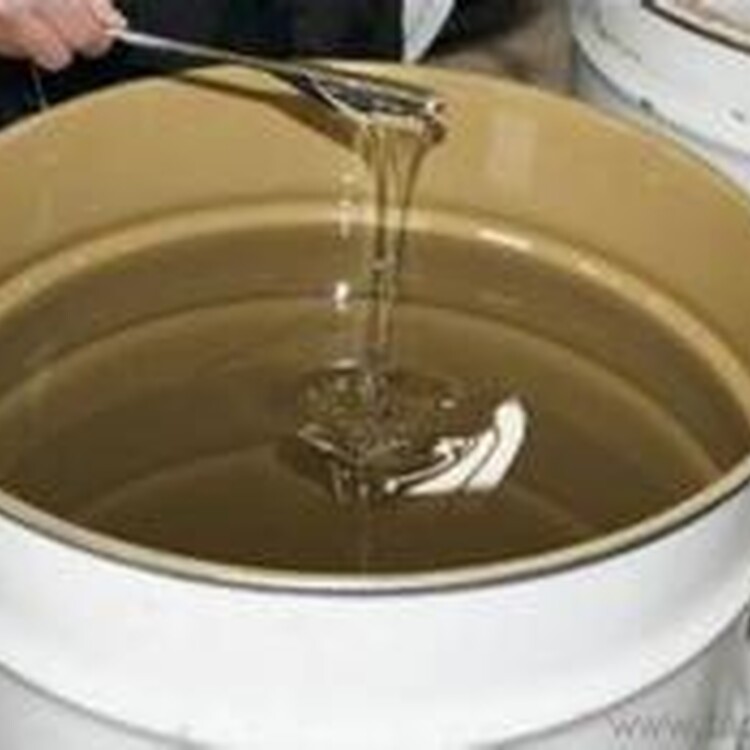
了制备高分子量(即高黏度)的二甲基硅油,工业上倾向于使用碱性催化剂。相反,酸性催化剂通常用于制备低分子量(即低黏度)的二甲基硅油。
反应活性顺序在碱性催化环境下,有机硅氧烷单元的反应活性顺序依次为:
D3(基硅氧烷)> D4(八甲基环四硅氧烷)> MD2M(十甲基四硅氧烷)> MDM(甲基二硅氧烷)> MM(六甲基二硅氧烷)。
而在酸性催化环境下,反应活性顺序则有所不同,依次为D3 > MM > MDM > MD2M > D4。
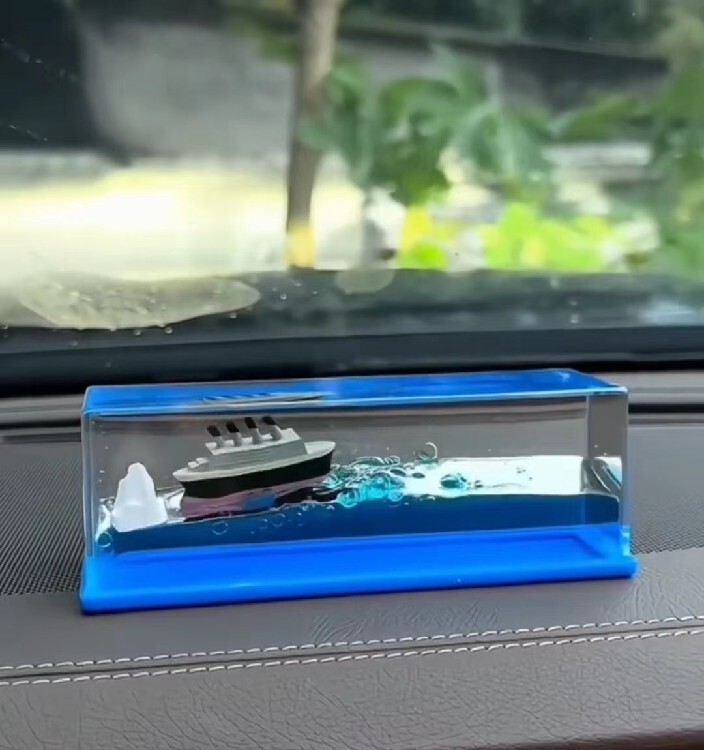
封端剂的选择
在采用碱性催化剂进行聚合时,为了防止生产过程中黏度的急剧增加,通常选用MD2M作为封端剂。MD2M具有较高的沸点(194℃),不易在反应过程中挥发,可以通过MM和D4在浓硫酸催化下制备。在酸性催化条件下,考虑到成本因素,通常会选择MM作为封端剂。
分子量的控制
二甲基硅油的平均分子量可以通过调整起始原料D(二氯二甲基硅烷的水解产物)和M单元(封端剂)的投料比例来控制。理论上,D和M单元的投料比例决定了硅油的平均聚合度。但由于平衡反应可能产生环状体,实际生产中还需要依赖于经验数据和实验结果。
生产实例
例如,为了合成具有100个硅氧烷链节的硅油(预期黏度约为120mm²/s),可以使用7400份硅氧烷和108份六甲基二硅氧烷作为原料。由于平衡体系中存在10%~15%的环状体,终得到的硅油可能会比较稀薄。这些环状体可以通过真空薄膜蒸发法去除,从而降低硅油中可挥发组分的含量,以满足应用领域对挥发性的要求。